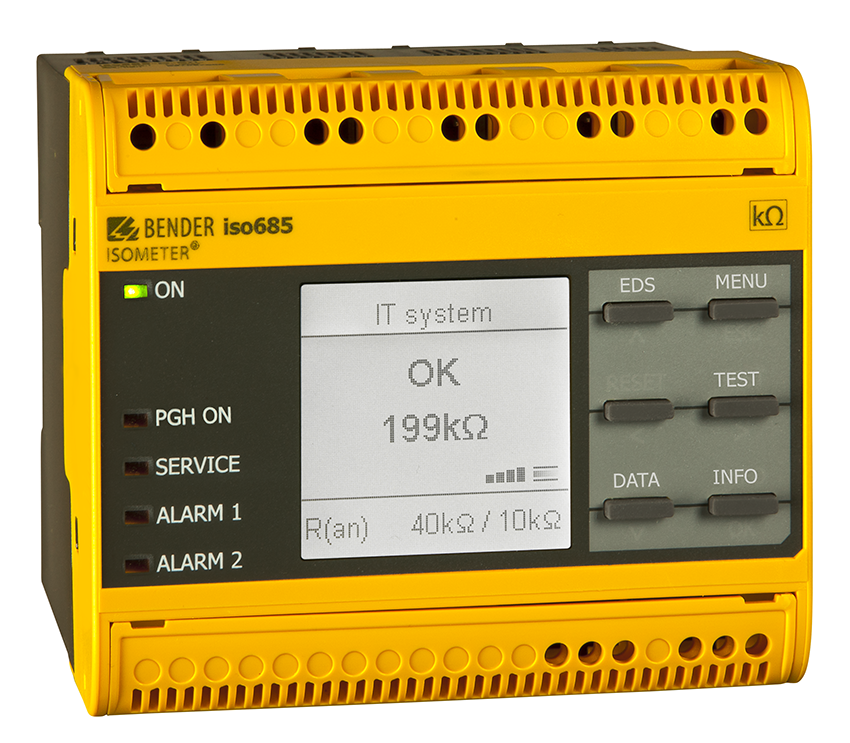
Maximising availability is paramount for profitable wind farm operation.
And if you’re a wind farm operator or engineer, you will want to know exactly when and where electrical faults are developing, so engineering maintenance can be planned in advance of failure occurring.
Knowing the existence of developing faults enables a proactive rather than reactive response, which is easier and more cost effective to manage, maximising availability and profitability of the asset and preventing downtime.
UK wind farm cable failure
In the UK offshore windfarms alone account for over 2,100km of inter-array cables, transporting over 8GW of generation. So far more than 50 inter-array cable failures have been recorded for fully commissioned sites. And as the sector continues to expand - 40GW of offshore wind is the target by 2030 – the number of failures will only increase.
How to maximise availability of wind farms? Array cable monitoring
Across industry applications, 90% of faults in power cables are phase to earth faults. Bender has capability and expertise in cable monitoring technology, and we now offer this solution for use in wind farm inter-array cables (onshore or offshore) to maximise availability for wind farm operators.
Proven solutions for cable monitoring
The UK rail industry utilises Bender technology to monitor signal power systems. The signalling power network is formed of a Principal Supply Point (equivalent to the collector station of a wind farm) where a DNO supply is transformed to 650V. The network is split into feeders (strings) which feeds Functional Supply Points (FSPs, or in this case, turbines) from which local supplies are taken to power signalling equipment. A typical network with a single transformer might have 6 feeders, each with 12 FSPs covering 10s of kilometres of track.
If the signalling supply drops, trains are unable to run, resulting in delays for passengers and penalties for operators. Bender rail signal power technology is installed at the principal supply point, and also at the functional supply points to continuously monitor the system for faults, giving advanced warning of which sections of cables are developing faults, so that they can be repaired before failure occurs.
Proposal for wind farm inter-array cable monitoring
We’ve traditionally been limited to medium voltage applications, up to ~15kV, but have now increased our capability to higher voltages. This means Bender can now offer a similar solution for inter-array cables.
We need your help to deploy it…
Equipment will be installed at the collector station (where strings of cables come together), and on turbines around the wind farm to split the cables up into sections.

The system will compare the status of the cable (values measured by the sensors) to a “healthy” pre-set value, and should the cable start to deteriorate this will be flagged and located to a cable or switchgear section. All information will be available remotely, using a proven communications solution.
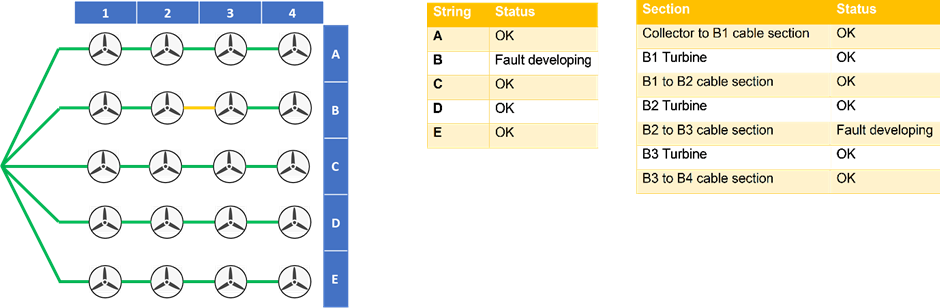
The granularity of the information depends where the equipment is installed – it will tell you if there is a fault developing between two monitored points. As such the system is easily scalable.
The wind farm operator will then have time to investigate the fault. If necessary, shutdown of the relevant array section can be planned, enabling repair of the fault in the most cost-effective manner.
The key point is that the array cable won’t suddenly trip without warning, leaving you with no generation, preventing repairs at short notice.
A common question:
“So, I won’t know exactly where the fault is. How is that of use to me?”
Yes, it won’t tell you within a metre the exact location of the fault. However, knowledge of the location of a fault to within a certain section before failure still has significant value:
- Experience tells us that a large proportion of failures occur at joints and in switchgear, not within the actual cable. We’re proposing a system that would tell you if the fault was developing within the switchgear, or in a cable section – making pinpointing these faults much easier.
- If your turbine strings are arranged in a ring, switching off a single cable section doesn’t have to result in lost generation. With the faulty cable switched out, you can then pinpoint the fault within the cable section, without loss of generation. We may be able to provide additional equipment to support you with this.
- In the worst-case scenario, you’ve got advanced warning ahead of a failure. You can plan for the moment when the section does fail and will be in a much better position to make the repair. As we gain experience in this sector, we may also be able to more accurately predict when a cable will fail.
Future projects?
This is a new application utilising proven Bender technology. We are looking to collaborate with interested industry partners to implement our technology into existing wind farms or to be designed into switchgear for future applications.
Contact
This blog was written by Will Heard (MEng, Electrical Engineer Bender UK). If you have any feedback or ideas for using this proposed solution, we would love to hear them.
About Bender UK
We are part of the Bender Group, and a growing UK electrical safety company with 70+ employees in the United Kingdom and Ireland.
We specialise in providing solutions for monitoring power systems, combining world leading devices manufactured at our factory in Germany with technical know-how to find something that works for you. We’re involved in lots of industries, and our technology is applicable in just about any application where availability of electrical power is crucial.
This article is for informational purposes only. Bender provides the information "as is" without warranty and is not responsible for its accuracy or reliability. No warranties are given regarding its suitability for any specific circumstances.